This was a great read, as I am a new homeowner and am looking to be well versed on my home insulation and HVAC so I know when I need to call a service and what a good deal is. Thanks for this!
Blog Post
Foam-In-Place Insulation: 7 Tips for Getting Injection and Spray Foam Right

There are two ways to site-install foam insulation: injection and spray. Injecting foam is most often done in closed cavities in retrofit applications; spray foam is most often done in open cavities and in new construction. The formulations and methods of installation are different for closed-cavity and open-cavity foam installations.
Photos: Henri Fennel (L); Peter Yost (R)One of my first research projects when I started at the NAHB Research Center in 1993 was looking into a new insulation: Icynene. We were evaluating its performance as a spray-applied, open-cavity insulation as well as an injection foam in closed cavities. I was enamored: this seemed to be a miracle insulation that installed itself, sealing up tight even in the toughest and most complicated building cavities.
At about the same time, the NAHB Research Center was developing an installation quality program for fiberglass batt insulation, notoriously difficult to get installed right. I scoffed; we would never need that for these foam-in-place systems!
Twenty-plus years later, it’s clear how wrong I was. What looked as easy as point-and-shoot with the foam gun has a lot of complexity. As insulation consultant Henri Fennell recently said to me, “Properly installing site foam insulation is way more challenging than fiberglass batts. It’s partly because performance expectations are high and partly because you are actually manufacturing onsite.”
Fennell has been injecting and spraying polyurethane foam insulation for more than 40 years. I recently got the chance to spend quite a bit of time with him at the Energy Center of Wisconsin’s Better Buildings, Better Business conference. Here are Fennell’s seven top tips for ensuring that manufactured foam insulation jobs—both injection and spray—get done right.
SUPPORT INDEPENDENT SUSTAINABILITY REPORTING
BuildingGreen relies on our premium members, not on advertisers. Help make our work possible.
See membership options »Tip #1: Understand the two systems
Part of getting site-manufactured foam right is understanding how injection and spray foam differ. Many of us have gained some exposure to the point-and-shoot method of applying spray foam, but foam injection also has a big place in the industry.
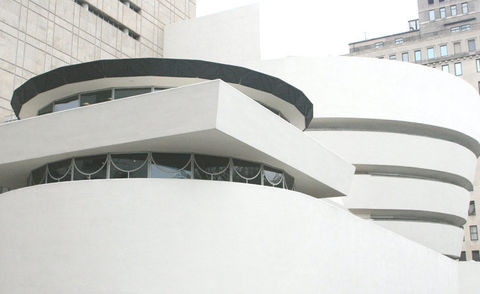
The striking rotunda of the Frank Lloyd Wright Guggenheim museum in New York City places all of the art in concave exhibition niches on the exterior of the building. The sloped floor and wall junction created a void and thermal bridge at this junction (see detail and photos below), which led to moisture and discoloration problems on the interior.
Photo: Mr. Littlehand. License: CC BY 2.0.He adds, “While most of us may be more familiar with—and therefore more ‘comfortable’ with—spray foam, foam injection has its place, particularly in retrofit. In fact, temperature, pressure, and personal protection requirements are all easier with injection than spray foam systems.”
Tip #2: Get the ratio right
Two-part spray- and injection-foam formulations require the right ratio of the “A” and “B” components for a proper chemical reaction to occur and thus for the insulation to be of good quality.
“Being off-ratio can result in poor foam quality and also toxicity issues,” notes Fennell. “This is a complex chemical process happening in the field, which requires care and full-time quality-assurance capabilities.”
There are a lot of variables that can affect the ratio and the mix—all of which can be addressed with the right equipment. For about $5,000 to $10,000, foam rigs can be outfitted with a “fault-interruption ratio” (when the mix goes off ratio, the rig shuts down) and a temperature monitor and will also produce printouts as proof of proper ratio.
Tip #3 (Spray foam only): Watch your lift thickness
A lift is a single layer of foam, sprayed in one pass. Each spray-foam product should be installed at the specific lift thickness recommended by the manufacturer. One manufacturer allows for as much as 6 inches, but most recommend or require lifts no greater than 1.5 to 2 inches.

Infrared-guided foam injection proved to be a relatively easy and effective fix to the problem.
Images: Henri FennellWith open-cell spray foams, there are typically no heat-of-reaction issues, but the expansion rate (about 100:1 compared to about 30:1 in closed-cell spray foam) can result in the formation of large voids in certain types of open-cell foam, affecting the material’s R-value.
“Controlling lift thickness in the field is a relatively simple matter, only requiring patience and attention to sequencing,” says Fennell.
That doesn’t hold true, however, in tricky spots the spray nozzle can’t reach well, like rim joists and outside corners. “It can be difficult, if not impossible, to follow manufacturer lift-thickness requirements for spray foam formulations in these locations,” relates Fennell, who recommends a couple of approaches: start the job with an injection mix to hit the tough spots first, and then purge to switch over and spray-foam the rest—or carry small injection-foam kits for convenience.
Tip #4: Get the substrate right
The temperature of the substrate is a big deal in winter installations; really cold substrates can pull enough heat out of the reaction that the spray foam does not expand properly or bond to the substrate adequately. Substrates that are too hot can also cause quality issues. Manufacturers provide high and low temperature limits for e
Thermal imaging helped guide the Guggenheim retrofit, initially identifying the problem and then guiding the injection process to complete the thermal and air barrier at the insulation voids.
Images: Henri FennellInstallers either need to match substrate requirements (such as moisture content or temperature) to the conditions as they occur, or modify the environment before installing. “We routinely used concrete curing blankets to insulate when we installed foam when cold-weather conditions required this approach,” says Fennell.
Some substrate materials can present challenges of their own, including bond-break materials like polyethylene sheeting. The high moisture content of wet framing and sheathing materials and pressure-treated lumber can also prevent bonding. “Each of these situations requires experience and often pre-installation pull-testing to get the installation correct,” cautions Fennell. “Allowing time to dry out the building, or for it to dry naturally, may be called for; plan ahead.”
Tip #5: Honor “wait” time, even when you don’t want to
“With each lift, think of the previous lift as the new substrate,” says Fennell.
This is because of heat and pressure. He explains that with spray foam, you’re waiting for the previous lift to cool enough, while with injection foam, you’re waiting for the previous layer to finish expanding.
In this way, patience translates to quality, but it’s easy to see how more time on the job could make proper installation more expensive.
Tip #6: Match the foam product to the application
Matching the properties of the foam product to the application is a big part of quality installations.
“It’s all about the chemical clock,” says Fennell. “A slow-rise injection foam reduces the pressure; a fast spray-foam system sticks to the substrate, even overhead. If you are injecting foam in a 6-inch, 100-foot conduit under a roadway, you will pick a different product and installation procedure than you would for an open framing cavity.”
Tip #7: Assure quality in the field

This mobile spray rig is setup in a box truck and looks more like a lab than a piece of jobsite equipment. Set up this way, the box can be climatized as needed. Note the setup includes ratio, usage, and temperature monitor with auto shut-off.
Photo: Henri FennellFennell uses a system of project-specific submittals and onsite quality-assurance methods to deliver good results, he says. “I have a suite of about a dozen or so submittals that I draw from for each foam project,” including product warranties, installation requirements, and safety data sheets, states Fennell (see Safety Sheets Getting New Format—And Some New Data). “My set of quality-assurance protocols is used during field applications to assure that the manufacturers’ recommendations are met throughout the course of the work.”
Is there an easier way?
Getting all this right may seem formidable, but consider the alternative: Fennell spends quite a bit of time remediating problem spray-foam installations on projects that do not use full documentation, comprehensive quality management, and fault-interruption ratio and temperature monitors.

This adhesion test is quality control assessing the bond between the installed foam and the substrate. Adhesion tests like this can be done prior to the installation as part of project assessment and done during or after job completion.
Photo: American Air Barrier AssociationPublished August 18, 2014 Permalink Citation
Yost, P. (2014, August 18). Foam-In-Place Insulation: 7 Tips for Getting Injection and Spray Foam Right. Retrieved from https://www.buildinggreen.com/blog/foam-place-insulation-7-tips-getting-injection-and-spray-foam-right
Comments
Spray Foam Insulation
The performance is in the details. This was a very good article from that viewpoint.
Add new comment
To post a comment, you need to register for a BuildingGreen Basic membership (free) or login to your existing profile.