Blog Post
Rigid Boardstock Insulation
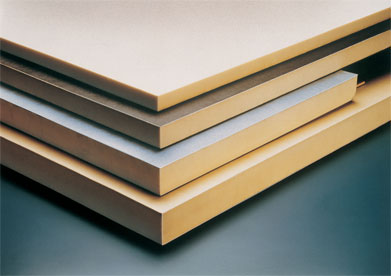
In this final installment about insulation we'll take a look at the family of rigid boardstock materials. Unlike fiberous or spray-foam insulation that is installed in wall or ceiling cavities between the studs, rafters, or joists, boardstock insulation is applied either on the interior or exterior surface, spanning across the framing.
The three most common types of rigid boardstock insulation are plastic foams: extruded polystyrene, expanded polystyrene, and polyisocyanurate. Extruded polystyrene (XPS), including the familiar light-blue Dow Styrofoam and Owens Corning's pink Foamular, is the most moisture-resistant of these three and is commonly used below-grade to insulate the exterior of foundation walls and under basement slabs. XPS provides an insulating value of R-5 per inch. Unfortunately, XPS (in this country) is still made with ozone-depleting HCFC blowing agents, which manufacturers are required to eliminate by 2010. Manufacturers of blowing agents, refrigerants, and other compounds have made great progress in eliminating substances that destroy the Earth's protective ozone layer in the stratosphere since the hole in the ozone layer above Antarctica was discovered in the 1980s. XPS is the only insulation material still made with ozone-depleting blowing agents.
Expanded polystyrene (EPS), also known as beadboard, is manufactured more locally by smaller companies than is XPS, and it can be purchased in a much wider range of dimensions, thicknesses, and densities. The most common EPS, with a density of about 1 pound per cubic foot, doesn't perform well below-grade, but it can be ordered at higher densities that do much better in such applications. For below-ground use, I recommend at least 1.5 pounds per cubic foot. Two-pound EPS is even better, with performance much closer to that of XPS. The most common low-density EPS insulates to about R-4 per inch. It is manufactured with pentane as the blowing agent, which does not harm ozone. EPS is the most common insulation material used in producing structural insulated panels, such as those made locally by Winter Panel Corporation and Foard Panel.
Polyisocyanurate is the highest-insulating boardstock option, providing R-6.0 to R-6.5 per inch. A special low-conductivity gas fills cells in the insulation, and foil facing slows down the loss of this gas or entry of air--a process that, unfortunately, reduces the R-value somewhat over time. This gas fill or "blowing agent" used to be an ozone-depleting compound, but manufacturers have shifted to ozone-safe blowing agents, usually pentane.
Polyisocyanurate is most commonly used for roofs and walls, but almost never below ground because it can absorb moisture.
In addition to these three rigid-foam boardstock materials, there are also rigid fiberglass and mineral wool boardstock insulation products. These are excellent in the right applications, but they are usually only available for commercial construction; they are not carried by most building supply centers serving residential builders and homeowners.
SUPPORT INDEPENDENT SUSTAINABILITY REPORTING
BuildingGreen relies on our premium members, not on advertisers. Help make our work possible.
See membership options »No matter what the type, boardstock insulation opens up some great opportunities for creating highly insulated--or superinsulated--walls. With new construction, I have long been a proponent of going well beyond a typical 2x6 wall insulated with cavity-fill fiberglass or cellulose. I believe that a reasonable R-value target for walls is R-35, and if I were building a new house I'd probably aim even higher. The easiest way to achieve such a high insulation level with wood-frame construction is a 2x6 wall with cellulose cavity-fill insulation and then an exterior layer of 3" of polyisocyanurate boardstock. However, that wall system, providing about R-35, will entail some extra effort with detailing:
First, the thicker walls will require extra trim around windows and doors. Second, you will probably have to combine two layers of boardstock insulation (a 1" layer and a 2" layer) to achieve the recommended three inches. Third, to provide racking strength (to hold the walls square), let-in metal bracing, or plywood or OSB sheathing, will be needed in addition to the boardstock insulation.
Lastly, to install siding, you'll need strapping with extra-long screws to secure it to the wall studs. (An added benefit is that the air space behind the siding that this strapping creates--called a rainscreen detail--improves the life of the siding and reduces the frequency of repainting.)
By providing such a thick layer of foil-faced boardstock insulation on the exterior, there is virtually no chance of moisture condensing within the 2x6 wall cavity; the cavity-fill cellulose insulation will be fully protected. Other approaches for achieving superinsulated houses, including SIP construction, double-stud walls, and special non-structural wall trusses that are hung on the outside of the structural wall, will be covered over the coming months in this column.
Published September 1, 2008 Permalink Citation
(2008, September 1). Rigid Boardstock Insulation. Retrieved from https://www.buildinggreen.com/blog/rigid-boardstock-insulation
Add new comment
To post a comment, you need to register for a BuildingGreen Basic membership (free) or login to your existing profile.